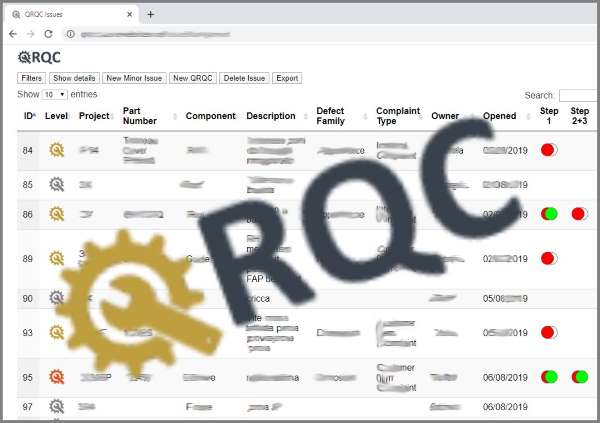
QRQC: Quick Response Quality Control
QRQC (Quick Response Quality Control)
is not only a quality control tool and method for troubleshooting but also an innovative concept in the field of global quality management.
QRQC integrates a simple and logical solution to a given production or business operation problem within 24 hours time and has applications
in many different segments along supply chains, including project management, manufacturing, logistics and others.
QRQC focuses on quality control to ensure that any problem is identified and isolated and that a solution is found and implemented quickly
and effectively.
QRQC is based on a Japanese concept known as San Gen Shugi, meaning “3 reals”. San Gen Shugi is a scientific method and concept
of problem solving and analysis with far-reaching applications. The 3 reals are defined as follows:
Real Situation – understanding what is really happening
Real Place – going to the real location of production
Real Problem – investigating the real problem or issue
QRQC is implemented throughout well defined steps
Step 1: Problem detection, identification and description
Step 2: Problem analysis: brainstorming about possible causes of the problem
Step 3: Identification of the root cause of the issue (through Ishikawa diagram)
Step 4: Definition of corrective and preventive actions and driving an action plan supported by Plan-Do-Check-Act (PDCA) problem-solving methodology
Step 5: Mining of lessons learnt for the future
The QRQC software supports those steps allowing easy information sharing and with an emphasis placed on “quick”:
bacause any problem with production should be communicated and shared quickly to the relevant person or team.
To know more about this solution, read the QRQC web app User Manual and the QRQC web app Administrator Guide.